2 MW Warwick Mills, USA
Plant specifications
Client: | Warwick Mills |
Location: | New Hampshire, USA |
Plant type: | Damp process |
Capacity: | 2 MW |
Fuel: | Wood chips |
Technology: | Biomass gasification technology for process industries |
Operational since: | 2014 |
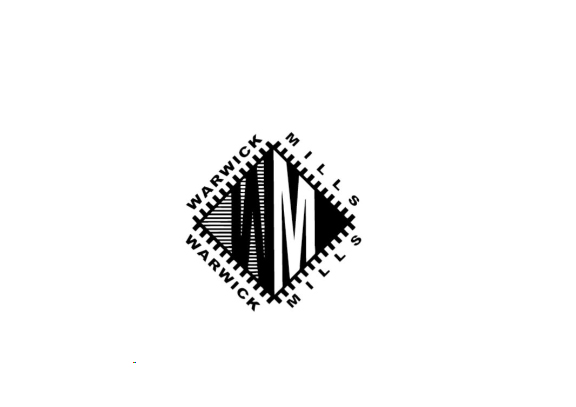
Industrial textile production in New Hampshire, USA
Warwick Mills is a manufacturer of high-tech textiles for body protection. At the factory, they design, manufacture and test advanced composite fibers that are used for protective clothing among others.
The biomass gasification furnace for Warwick Mills was produced in Denmark and shipped to the US in one piece. The client subsequently independently incorporated the furnace into their existent production facilities at the factory.
Plant Manager Charlie Howland and the President of CEM Services Chris Cutting enthusiastically explain the integration of Dall Energy’s biomass gasification furnace. They emphasize the following:
- Dall Energy’s design is not only efficient regarding biomass energy production, but also for destroying VOCs.
- Their excitement about the prospect of using entire wood chips as fuel for the biomass gasification furnace.
- The very low CO, NOX and particle emissions.
"Dall's system is like a mustang for wood chips"
- Chris Cutting, president of CEM Services
Low emissions and high particle removal efficiency
The plant is in commercial operation and produces environmentally friendly heat for the factory. At the handover, a performance test measured the removal efficiency in terms of eliminating organic compounds from the combustion air, which was ventilation air from the industrial processes.
A removal efficiency of over 99.8% was measured, which meant that the organic compounds in the flue gas were reduced to below the level that could be measured outdoors due to the natural sources. The other emissions were also very low: NOx: 40 ppm, CO: 10 ppm, dust: 10 mg/Nm3. This was even without the plant having installed any kind of flue gas filters, cyclones or catalysts.
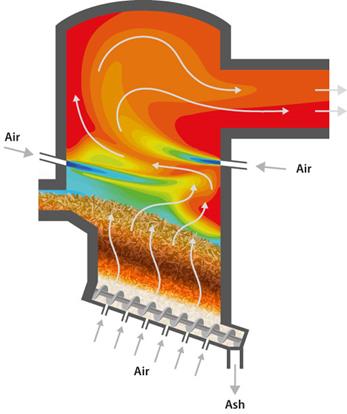
Energy for industry
Sustainable heat and VOC destruction
Since 2014 the furnace has covered two applications for the factory: provision of sustainable heat that covers the factory’s needs and additionally reducing the quantity of organic compounds from the ventilation air to comply with the local law requirements by a good margin.